Posted by
sino seo Nov 14
-
Category:
Technology
-
8 views -
0 comments
-
0 likes
Selecting the right casting alloy for a grooved pipe coupling involves several key considerations:
1. Mechanical Properties
- Strength: Ensure the alloy has adequate tensile and yield strength to withstand operational pressures.
- Ductility: A good level of ductility is important to avoid brittle failure.
2. Corrosion Resistance
- Consider the environment where the coupling will be used (e.g., chemical exposure, moisture).
- Alloys like stainless steel or certain aluminum alloys may be preferable for corrosive environments.
3. Thermal Properties
- Assess the thermal conductivity and expansion characteristics, especially if the coupling will be exposed to temperature fluctuations.
4. Compatibility
- Ensure that the alloy is compatible with the pipes being connected. This includes considering galvanic corrosion issues if dissimilar metals are used.
5. Casting Method
- The chosen alloy should be suitable for the casting method (sand casting, investment casting, etc.) to ensure good surface finish and dimensional accuracy.
6. Cost and Availability
- Evaluate the cost of the alloy and its availability in the market to ensure it meets budgetary constraints.
7. Standards and Certifications
- Verify that the alloy meets relevant industry standards (e.g., ASTM, ISO) for quality and performance.
8. Testing and Performance History
- Review previous performance data or test results for the alloy in similar applications to gauge reliability.
Common Alloy Choices
- Ductile Iron: Good strength, ductility, and corrosion resistance for many applications.
- Aluminum Alloys: Lightweight and corrosion-resistant but may have lower strength.
- Stainless Steel: Excellent corrosion resistance and strength, suitable for harsh environments.
By carefully evaluating these factors, you can select an appropriate casting alloy for your grooved pipe couplings that meets the specific demands of your application.
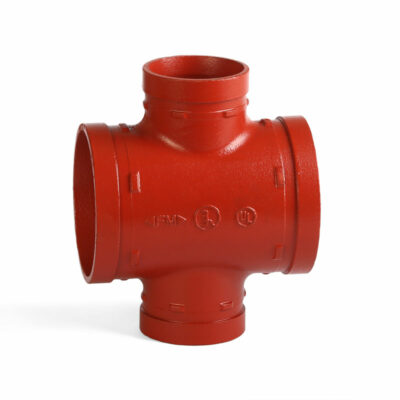